IOLINK模块是工业自动化领域中用于实现设备间智能通信的核心组件,其本质是一种标准化的数字通信接口技术,基于 IO-Link协议(IEC 61131-9标准),在传感器、执行器与上层控制系统(如PLC)之间建立高效、灵活的双向数据通道。以下从多个维度详细解析其功能、原理、应用及价值:
一、IOLINK模块核心功能与工作原理
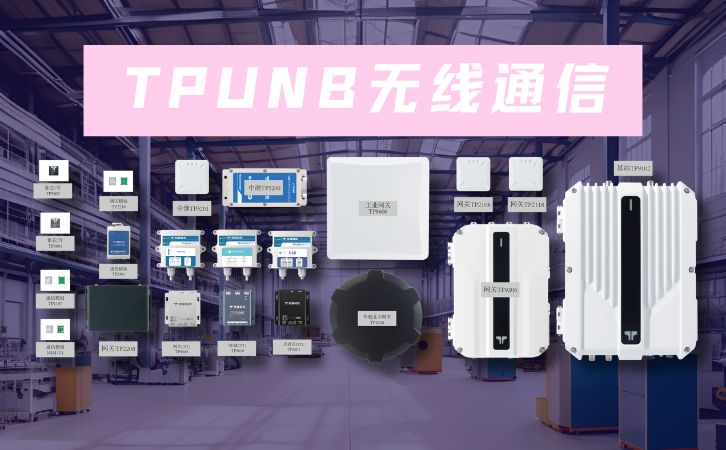
1. 设备互联桥梁
IOLINK模块充当传感器/执行器与控制系统的接口,通过标准化的三线电缆(电源24V、信号线、接地)实现点对点通信。它支持多种设备类型(光电传感器、气动阀、RFID读写器等),统一了不同厂商设备的接入方式,解决兼容性问题。
2. 双向数据传输
过程数据:实时传输设备状态(如温度、压力、开关量)至控制系统,循环时间可低至2ms(38.4kbps速率)。
参数数据:远程配置设备参数(如灵敏度、延迟时间),无需人工现场调试。
诊断数据:提供设备故障预警、运行状态监测,支持预测性维护。
3. 智能运维支持
参数备份与恢复:模块自动备份设备参数至主站,更换设备时一键恢复,减少停机时间。
热插拔功能:支持运行中更换设备,不影响系统连续性。
二、技术特性与优势
1. 标准化与兼容性
采用M12连接器和标准电缆(最长20米),兼容传统I/O设备(通过SIO模式)。
IODD文件(IO Device Description) 确保不同厂商设备的即插即用,通过统一数据库(如IODD Finder)管理设备信息。
2. 高效通信能力
传输速率支持 4.8kbps(COM1)、38.4kbps(COM2)、230.4kbps(COM3) 。
数据缓冲区可调(2–32字节),适应不同数据量需求。
3. 简化系统集成
减少布线复杂度:传统模拟信号需独立线路,而IOLINK通过单根电缆传输多类数据。
无需专用网关:直接接入现场总线(如PROFINET、EtherNet/IP)。
三、典型应用场景
1. 智能工厂监控
汽车制造:实时监测冲压机压力、焊接温度,动态调整气阀开度。
电子装配:通过RFID传感器追踪产品流向,优化生产流程。
2. 预测性维护系统
分析电机振动数据,提前识别轴承磨损,减少意外停机。
3. 柔性生产线
快速更换传感器/执行器(如食品加工线切换产品规格),支持小批量定制化生产。
4. 能源管理
采集设备能耗数据,优化空压机、照明系统运行策略,降低能源成本。
四、与传统技术的对比
特性 | 传统I/O技术 | IOLINK模块 |
---|---|---|
数据传输 | 仅开关量/模拟量信号 | 支持过程数据、参数配置、诊断信息 |
布线复杂度 | 多线缆、专用接口 | 三线标准化电缆 |
设备更换 | 需手动重新调试参数 | 参数自动备份与恢复 |
诊断能力 | 有限 | 实时故障预警与根因分析 |
扩展灵活性 | 硬件改造难度大 | 即插即用,支持热插拔 |
五、面临的挑战与未来趋势
1. 当前挑战
数据安全:需加强通信加密(如TLS)防止未授权访问。
抗干扰能力:复杂电磁环境中需优化信号稳定性。
2. 技术演进方向
AI集成:结合机器学习分析设备数据,实现自适应控制。
OPC UA融合:通过OPC UA Pub/Sub模型提升跨平台数据互通性。
边缘计算:在模块端预处理数据,减少云端负载。
六、总结
IOLINK模块是工业4.0的关键使能技术,通过标准化通信协议解决了设备“最后一米”的数字化难题。其核心价值在于:
✅ 提升生产效率(减少停机、优化流程)
✅ 降低运维成本(远程调试、预测性维护)
✅ 增强系统灵活性(快速适配产线变更)
随着工业物联网(IIoT)发展,IOLINK将进一步推动智能制造向数据驱动、自适应控制的范式演进。